Die Casting Automotive: Revolutionizing the Automotive Industry
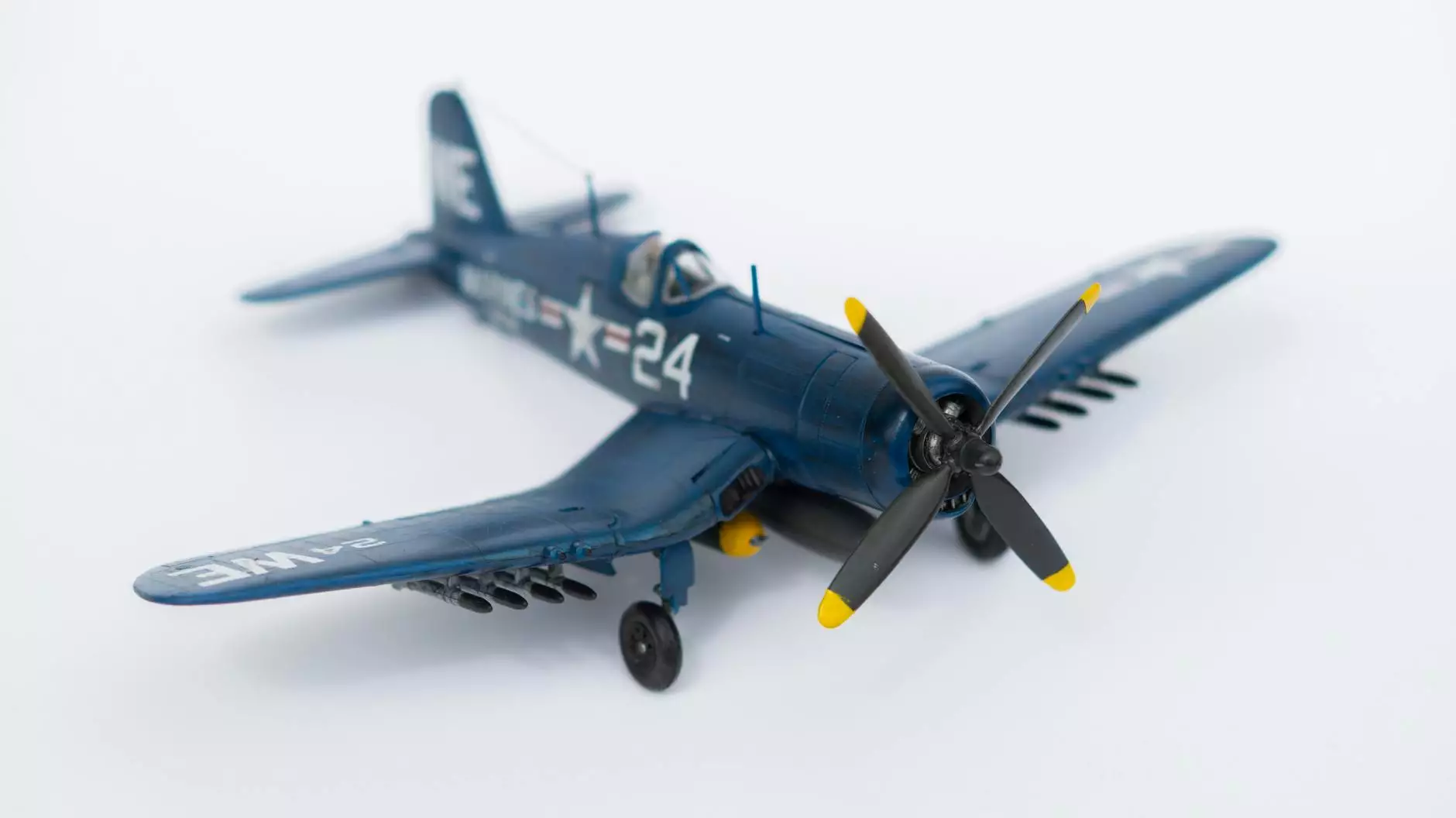
Die casting automotive is at the forefront of technological advancement in the automotive industry. This manufacturing process is reshaping the production of vehicles, leading to higher efficiency and superior product quality. In this comprehensive article, we will delve into the intricacies of die casting, its advantages, applications, and the future it promises for automotive manufacturing.
Understanding Die Casting
Die casting is a process that involves forcing molten metal into a mold cavity under high pressure. This process is ideal for producing complex shapes with fine details, making it particularly valuable in the automotive sector. The most commonly used metals in die casting are aluminum, zinc, and magnesium due to their lightweight and strong properties.
The Importance of Die Casting in Automotive Manufacturing
In the automotive world, the demand for lightweight yet durable components is ever-increasing. Here are some reasons why die casting plays a crucial role:
- Weight Reduction: Automakers are striving to reduce vehicle weight to improve fuel efficiency. Die casting allows for the production of lightweight components without sacrificing strength.
- Complex Geometries: The precision offered by die casting means manufacturers can create intricate designs, allowing for innovative automotive features and aesthetics.
- Cost-Effectiveness: Despite the initial costs associated with making molds, the high-volume production capabilities of die casting ultimately lead to lower per-unit costs.
- Reduced Waste: Die casting offers higher material utilization rates compared to other manufacturing processes, thereby reducing waste and lowering material costs.
Key Advantages of Die Casting in the Automotive Sector
Choosing die casting as the manufacturing method for automotive components comes with numerous advantages:
1. Exceptional Dimensional Accuracy
Die casting provides a high level of dimensional precision. Parts produced through this method are less likely to require extensive machining or finishing processes. This accuracy ensures parts fit properly and function effectively, which is critical in automotive applications.
2. Superior Surface Finish
The process yields parts with a smooth surface finish, often requiring little to no additional finishing. This not only saves time and money but also enhances the aesthetics of the automotive component.
3. High Production Rates
Die casting is capable of high-volume production, making it suitable for the mass manufacturing of automotive components. This efficiency allows manufacturers to meet market demands swiftly.
4. Variety of Metals and Alloys
Aluminum, zinc, and magnesium are the most commonly used materials, each providing unique properties such as corrosion resistance, strength-to-weight ratios, and thermal conductivity, ideal for different automotive applications.
Applications of Die Casting in Automotive Industry
The versatility of die casting makes it suitable for various automotive components:
1. Engine Components
Die casting is extensively used to manufacture critical engine components such as cylinder heads, engine blocks, and intake manifolds. The strength and lightweight nature of the materials help in enhancing engine efficiency.
2. Transmission Housings
Transmission housing made from die-cast aluminum or magnesium is not only lightweight but also provides necessary strength and rigidity, crucial for performance and durability.
3. Structural Components
Components such as cross members, brackets, and frame components benefit from the robust nature of die-cast parts, offering excellent load-bearing capabilities.
4. Aesthetic Parts
Die casting is also used for producing the exterior parts of vehicles, including trims, grills, and housings, showcasing the aesthetic flexibility it offers to designers.
The Advanced Die Casting Process
Understanding the die casting process involves several stages:
1. Mold Design
The first step in the process is designing the mold. Molds are typically made from steel or iron and need to be highly durable to withstand repeated cycles.
2. Melting the Metal
The metal is heated in a furnace until it reaches a molten state. The choice of melting temperature varies depending on the type of metal used.
3. Injection of Molten Metal
The molten metal is then injected into the mold cavity under high pressure. This step is critical as it ensures that the molten metal fills every part of the mold.
4. Cooling and Ejection
After the metal has cooled and solidified, the mold opens and ejects the finished part. This process often happens quickly, allowing for high production rates.
Quality Control in Die Casting
Maintaining quality is paramount in die casting. Several measures are taken to ensure that automotive components meet stringent industry standards:
- Material Testing: Raw materials are tested for their chemical composition and mechanical properties before use.
- Dimensional Inspection: Components undergo rigorous inspections to ensure they adhere to specified tolerances.
- Surface Quality Checks: Techniques such as ultrasonic testing or X-ray inspection are utilized to detect internal defects.
- Final Product Testing: Finished products are subjected to checks simulating actual operating conditions to ensure reliability.
Future Trends in Die Casting for Automotive Applications
The die casting industry, particularly within the automotive sector, is continuously evolving to meet future challenges:
1. Advancements in Materials
Research is ongoing into new alloy formulations and materials that can offer better performance, strength, and lighter weight. This development is particularly important for the push towards electric vehicles.
2. Automation and Industry 4.0
Automation technologies are being integrated into die casting processes to increase efficiency, reduce labor costs, and improve quality control measures.
3. Sustainability Efforts
With increasing focus on environmental responsibility, die casting operations are looking to minimize waste and energy consumption, contributing to more sustainable manufacturing practices.
4. Lightweighting Initiatives
As automakers strive to produce lighter vehicles to improve efficiency and reduce emissions, die casting will play a pivotal role in the development of new lightweight components.
Conclusion
In conclusion, die casting automotive is a key player in the evolution of the automotive industry. Its ability to produce high-quality, complex, and lightweight components makes it indispensable for modern vehicle manufacturing. As technology advances and the automotive landscape shifts towards sustainability and efficiency, die casting will undoubtedly continue to lead the way in innovation and quality.
For businesses looking to harness the benefits of die casting in automotive applications, partnering with experienced metal fabricators can ensure access to the best practices and state-of-the-art technology, ultimately driving success in the competitive automotive market.