Understanding Injection Molding Manufacturing
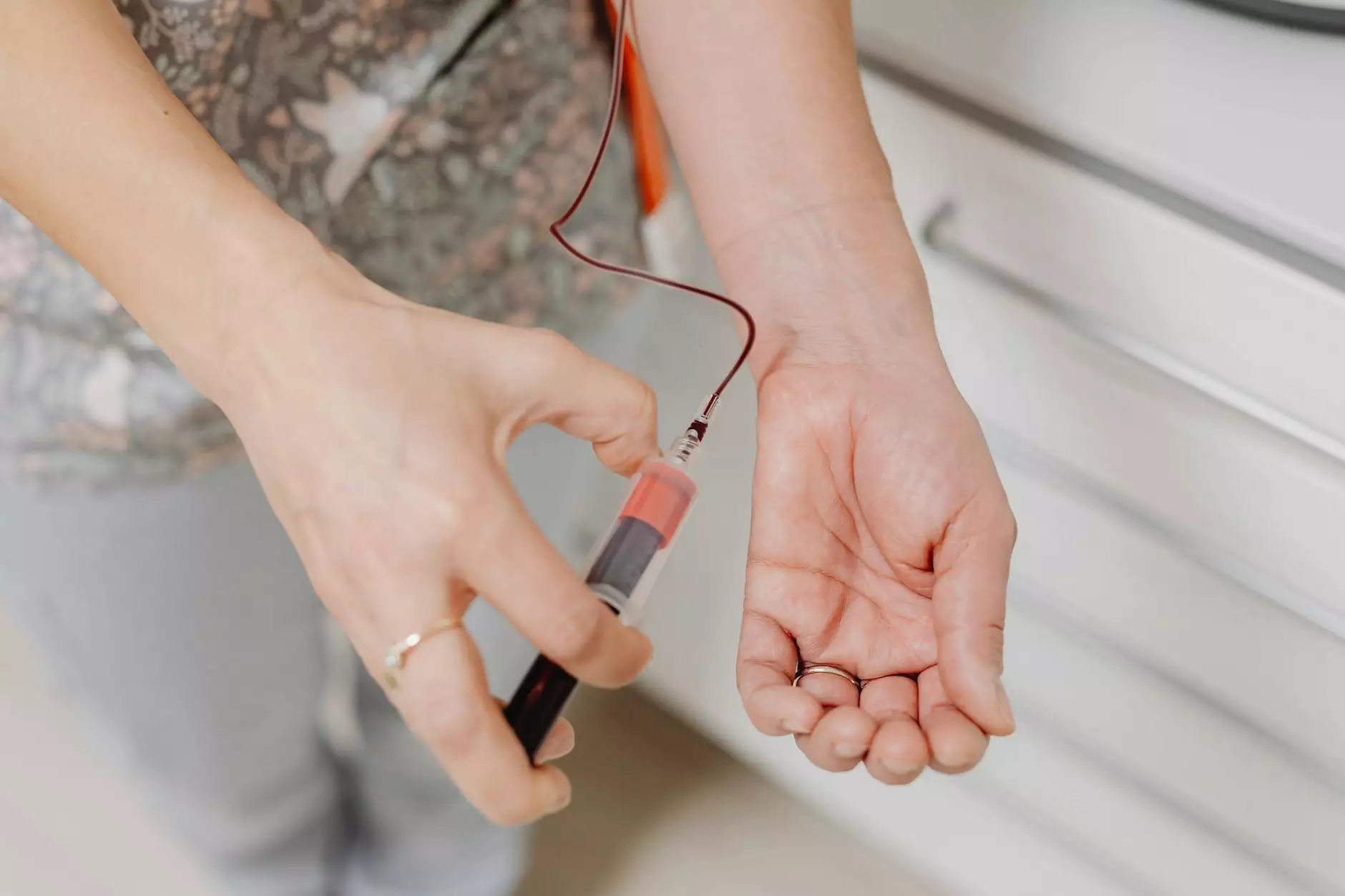
The realm of injection molding manufacturing is a sophisticated and critical component in the landscape of modern industry. As businesses strive to optimize efficiency and enhance product quality, injection molding emerges as a preferred choice for many manufacturers. This article serves as a detailed guide into the world of injection molding, its process, advantages, applications, and its significant role in the sector of metal fabricators.
What is Injection Molding?
Injection molding is a manufacturing process used to produce parts by injecting molten material into a mold. This process employs various materials, predominantly plastics, but it is also applicable in the production of metals and even ceramics. The main components of injection molding technology include:
- Injection Unit: This consists of a screw and barrel that melt the material and inject it into the mold.
- Clamping Unit: This provides the required pressure to clamp the mold together during injection.
- Mold: The mold is a hollow block, often made of steel or aluminum, where the molten material takes its shape.
The Process of Injection Molding Manufacturing
The process of injection molding manufacturing can be outlined in a series of systematic steps:
1. Material Selection
The choice of material is paramount. Common materials include thermoplastics, thermosets, and elastomers. Each material presents unique properties, impacting the final product's durability and functionality.
2. Mold Design and Fabrication
An intricate mold design is crucial for the success of the injection molding process. It involves:
- Comprehensive design planning to facilitate the flow of material.
- Consideration of draft angles and tolerances to ensure the easy release of the molded part.
- Fabricating molds using high-precision machinery to achieve accurate dimensions.
3. Melting and Injection
Once the mold is ready, the selected material is fed into the injection unit, where it is heated and melted. This molten material is then injected into the mold under high pressure.
4. Cooling
After injection, the molten material is allowed to cool and solidify, taking the shape of the mold. This cooling phase can significantly affect the quality of the finished product.
5. Ejection
Once fully cooled, the mold opens, and the solidified part is ejected, typically using ejector pins. This step requires precision to prevent damage to the part.
6. Finishing
After ejection, the parts may require additional finishing processes, including trimming, painting, or secondary processes, to enhance their appearance and functionality.
Advantages of Injection Molding Manufacturing
Injection molding offers numerous advantages that make it indispensable for metal fabricators and various other manufacturing sectors:
- High Efficiency: The process allows for rapid production rates, enabling mass production of complex shapes and designs.
- Cost-Effectiveness: Once the mold is created, the cost per unit decreases with increased production volume.
- Precision and Detail: Injection molding can produce parts with tight tolerances and intricate designs, crucial for high-performance applications.
- Material Versatility: A wide array of materials can be used, ranging from thermoplastics to metals, allowing for greater innovation in design.
- Reduced Waste: The precision of the process minimizes excess material and reduces waste, contributing to sustainability.
Applications of Injection Molding in Metal Fabrication
In the context of metal fabricators, injection molding finds diverse applications:
Automotive Industry
Injection molding is pivotal in producing various automotive components, such as dashboards, panels, and housings. The industry demands durability and precision, making injection molding an ideal choice.
Consumer Electronics
The consumer electronics sector relies heavily on customized plastic parts, from phone cases to intricate internal components. The ability to produce these parts at scale, with exceptional accuracy, enhances their value.
Medical Devices
In healthcare, precision is crucial. Injection molding enables the manufacturing of complex components for medical devices, ensuring sterility and compliance with stringent regulations.
Industrial Equipment
Various industrial applications benefit from injection molded components, including housings, gears, and brackets that demand high strength and precise dimensions.
Challenges in Injection Molding Manufacturing
While injection molding has significant advantages, it also presents challenges that manufacturers must address:
1. High Initial Costs
The costs associated with designing and fabricating molds can be high, which may deter small businesses from leveraging this technology.
2. Design Complexity
Designing injection molds requires expertise and can be time-consuming, especially for intricate parts that involve multi-cavity molds.
3. Material Limitations
Not all materials are suitable for injection molding. Some polymers may not flow well under high pressure, necessitating careful material selection.
Future Trends in Injection Molding Manufacturing
The future of injection molding manufacturing appears promising, with several trends shaping its evolution:
1. Increased Automation
Automation in the injection molding process enhances efficiency and reduces labor costs. Automated systems can handle everything from loading materials to monitoring the injection process.
2. Sustainable Practices
Manufacturers are increasingly adopting sustainable practices, such as using recycled materials and energy-efficient machines, to reduce their environmental impact.
3. Advanced Materials
Research into advanced materials, including bioplastics and high-performance composites, is paving the way for innovative applications in diverse sectors.
4. 3D Printing Integration
Integrating 3D printing with injection molding enables rapid prototyping, allowing businesses to test and refine designs quickly before committing to large-scale production.
Conclusion
Injection molding manufacturing is a vital process in the production landscape, particularly for metal fabricators. Its advantages, including efficiency, precision, and cost-effectiveness, make it a preferred choice across various industries. Understanding the complexities of this process, its applications, and its future trends will empower businesses to leverage injection molding effectively and drive innovation in their manufacturing endeavors.
As we dive deeper into the world of manufacturing, it is clear that injection molding will continue to play a critical role in shaping how products are designed and produced. For businesses looking to stand out, mastering the intricacies of this process is essential for long-term success and competitiveness.