Maximizing Efficiency with Label Applicators for Businesses
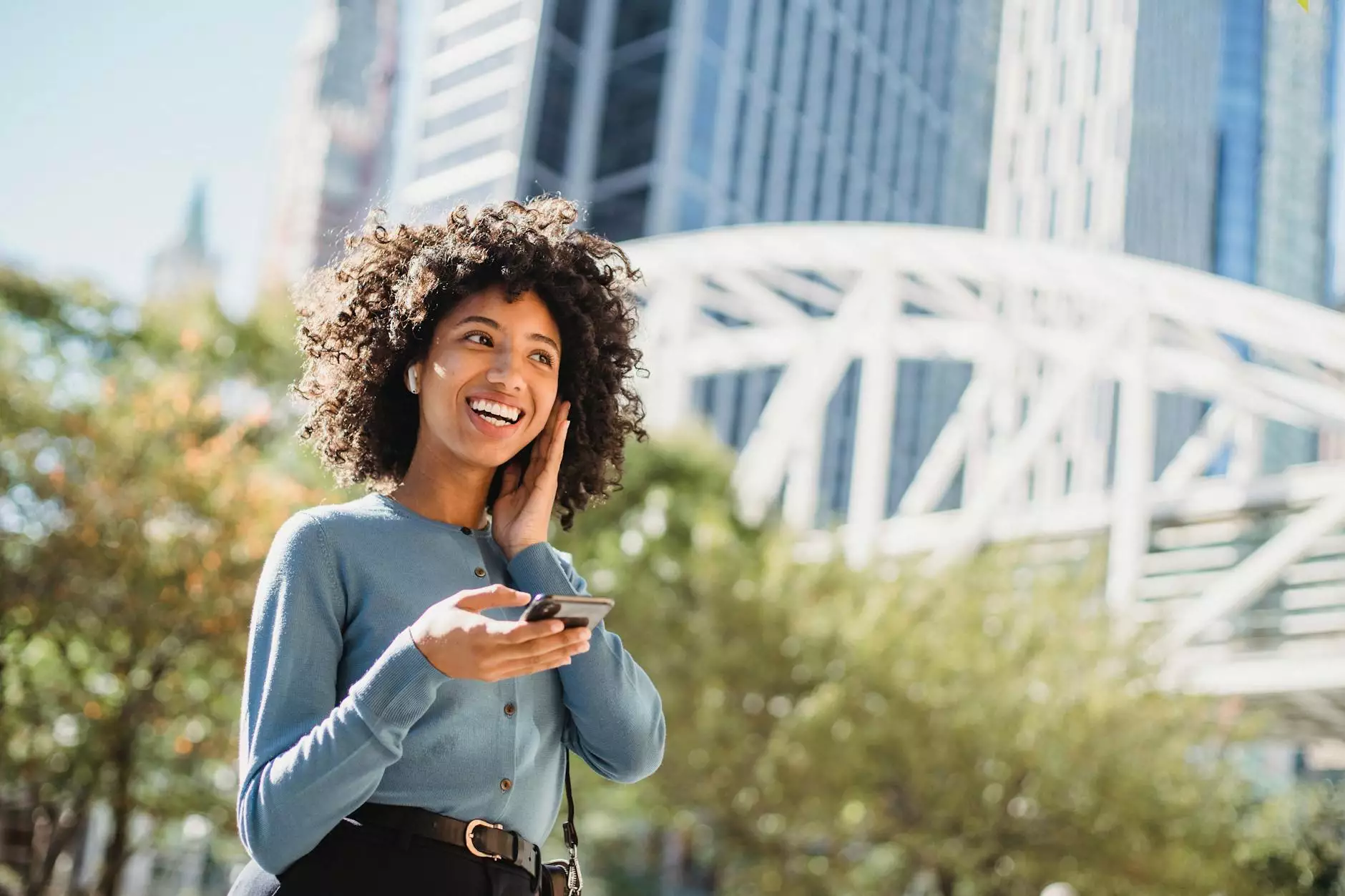
In today's fast-paced industrial landscape, businesses must streamline their processes and enhance productivity to stay competitive. An essential component of this efficiency is the use of label applicators. These powerful tools not only improve the accuracy of labeling but also significantly decrease labor costs and increase throughput. This article explores the myriad benefits of label applicators, their various forms, and how they can be seamlessly integrated into your operations.
The Importance of Labeling in Business
Labeling plays a crucial role in the logistics and supply chain of any business. Accurate labeling can affect inventory management, product identification, and shipping logistics. A well-labeled product is not only easier to find in the warehouse but also ensures that customers receive the correct items. Here are some compelling reasons why effective labeling is vital:
- Improved Accuracy: Reduces human error in product identification.
- Inventory Management: Aids in tracking and managing inventory levels efficiently.
- Enhanced Compliance: Meets regulatory requirements, especially in sectors like pharmaceuticals and food packaging.
- Brand Recognition: Provides an opportunity for branding and marketing directly on the product.
What are Label Applicators?
Label applicators are mechanical devices designed to automate the process of applying labels to products, containers, or packaging. They can range from simple manual devices to complex automated systems that are integrated into packaging lines.
These devices can apply labels at high speeds while ensuring precision, thereby optimizing both productivity and accuracy. Label applicators can be categorized into several types:
Types of Label Applicators
- Manual Label Applicators: Typically used for low volume applications, these require operators to apply the label by hand. They are cost-effective and suitable for small businesses.
- Semi-Automatic Label Applicators: These machines require some manual input but significantly speed up the process compared to manual methods.
- Fully Automatic Label Applicators: Ideal for high volume packaging lines, fully automatic label applicators can apply labels at speeds up to 600 products per minute.
- Print and Apply Systems: These combine printing and application in one machine, allowing businesses to print variable data such as barcodes or batch codes on-the-fly.
Benefits of Using Label Applicators
1. Increased Productivity
By incorporating label applicators into your production line, you can vastly improve the speed at which products are labeled. This increase in throughput can lead to shorter lead times and improved customer satisfaction.
2. Enhanced Quality Control
Label applicators reduce the risk of human error, ensuring that every product is labeled accurately. This consistency is critical in maintaining product integrity and compliance with industry regulations.
3. Cost Efficiency
While the initial investment in an applicator may seem significant, the reduction in labor costs and increased output leads to a quick return on investment. Companies often find that automating the labeling process frees up employees to focus on more critical tasks.
4. Flexibility and Versatility
Modern label applicators can handle a variety of label sizes, materials, and shapes, which provides flexibility in production. This versatility allows businesses to adapt swiftly to market changes without the need for expensive overhaul processes.
Application of Label Applicators Across Industries
Label applicators are not confined to a single industry; their application spans multiple sectors. Here’s a look at how different industries can benefit from these valuable tools:
1. Food and Beverage Industry
In the food industry, accurate labeling is essential for compliance with health regulations. Label applicators help ensure that all nutritional information and allergen warnings are consistently applied, minimizing the risk of costly recalls.
2. Pharmaceuticals
Labeling in the pharmaceutical industry is governed by strict regulatory standards. Label applicators assist in affixing labels that provide crucial dosage information and warnings, ensuring patient safety and regulatory compliance.
3. Retail and E-commerce
For retailers and online sellers, product labeling impacts brand perception and customer experience. Automated label applicators allow for uniform branding across products, enhancing overall presentation and professionalism.
4. Electronics
In the electronics industry, labeling is vital for warranty information, serial numbers, and product specifications. Label applicators ensure that these critical labels are applied efficiently and accurately.
Selecting the Right Label Applicator
Choosing the appropriate label applicator for your business requires a thorough understanding of your specific needs. Here are some factors to consider:
- Volume of Production: Assess how many products you need to label daily.
- Label Size and Type: Determine the sizes and materials of the labels you will be using.
- Product Type: Consider the surface and shape of the products being labeled.
- Integration Capabilities: Ensure that the applicator can integrate with existing production and packaging lines.
Integrating Label Applicators into Your Business
Successfully incorporating label applicators into your operations requires careful planning and execution. Here are actionable steps to ensure a smooth integration:
1. Evaluate Your Current Process
Analyze your existing labeling process to identify pain points and opportunities for improvement. Determine where automation can provide the most significant benefits.
2. Involve Your Staff
Engaging your employees in the selection and implementation process can ensure that their insights are integrated, leading to a smoother transition and better acceptance of the new technology.
3. Train Your Team
Once your label applicator is installed, ongoing training is essential. Regular training sessions will help staff familiarize themselves with the technology and troubleshoot common issues.
4. Monitor Performance
After implementation, closely monitor the performance of the label applicator. Use KPIs such as labeling speed, accuracy, and downtime to assess its effectiveness.
Future Trends in Label Applicators
The field of labeling technology is continuously evolving. Here are some future trends to watch for:
1. Smart Labeling Technology
As the Internet of Things (IoT) gains traction, smart label technologies that incorporate tracking and data analytics are likely to emerge, enhancing the ability to manage inventory effectively.
2. Sustainability in Labeling
Environmental concerns are increasingly influencing labeling materials and processes. Future label applicators will likely focus on sustainable materials that reduce waste and environmental impact.
3. Customization and Personalization
The demand for personalized consumer experiences is rising. Label applicators that can easily switch between different label designs and customizations will become more in demand.
Conclusion
In conclusion, label applicators play a pivotal role in enhancing the efficiency of business operations across various industries. From improving accuracy and productivity to providing flexibility and cost savings, the benefits are numerous. As technology continues to advance, staying updated on the latest trends and innovations in labeling will be vital for maintaining a competitive edge.
For businesses aiming to bolster their labeling processes, investing in a label applicator from reputable suppliers like omegabrand.com can be a strategic move. Embrace the future of labeling and witness the transformative effect it can have on your business.